Closed material cycles are the key to environmentally friendly and responsible use of plastics. In particular, the recycling of PET drinks bottles has distinguished itself as a shining example in recent years. 94% of all PET drinks bottles are now recycled, and the recovery rate is even close to 100%. In addition, there is a clear trend towards the use of recycled material: a PET bottle already consists of 30 to 50% recyclate today.
Services at a glace
- Expertise in the management of the material flow as well as in the subsequent processing
- Extension of the life of the material through reuse
- Conservation of natural resources such as water and oil
- Reduction of CO2 emissions compared to the production of new material by up to 50%
The recyclate generated in the URRC process meets the following requirements:
- Suitable for mass production of drinks bottles with high-performance injection-moulding machines possible
- Easy filling in the drinks industry guaranteed
- Unrestricted storage properties (e.g. stackability, compression resistance)
- Does not differ visually from new materials
- Certification of food-grade quality from renowned testing institutes
Services for
Industry, trade
Contact
Veolia PET Germany GmbH
Amerigo-Vespucci-Platz 1
D-20457 Hamburg
Tel.: +49 (0) 40 78 101 672
Fax: +49 (0) 40 78 101 690
Bottle-to-bottle recycling
Through the deposit system for single-use bottles, more than 4 billion PET bottles find their way into our European plants every year. At our sites, we use a patented multi-stage URRC process to convert the plastics into food-grade recyclates, which can be used to produce new bottles. Veolia PET Germany GmbH specialises in a bottle-to-bottle·process that is not only environmentally friendly, but one of the most efficient processes in the world. It is impressing in technical and ecological terms.
Many drinks manufacturers and bottling companies in Germany rely on the consistent and food-grade quality of our recyclate.
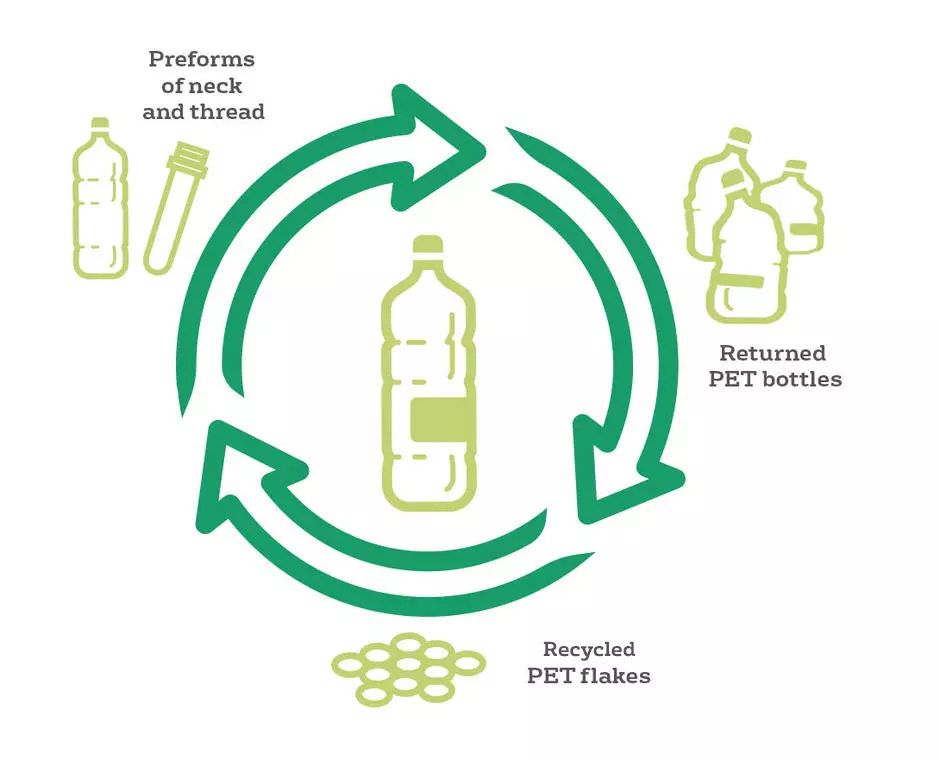
After foreign objects such as drinks cans have been removed, the bottles are crushed into flakes, the labels are removed and the caps are skimmed off in a tank. The PET is degassed in a complex mechanical-chemical process and the surface is cleaned. In the process, flakes are mixed with caustic soda, which dissolves the top layer and any impurities. During this approximately three-hour process, the flakes rotate in a 26-metre-long rotary kiln with different temperature levels. After a final rinse with drinking water, the recovered PET is food-grade again. Finally, the flakes are sorted, dried and filled into big bags. In order to guarantee consistently high quality, most of our production facilities have their own laboratories in which important parameters in terms of food suitability and processability are continuously measured.
Packed in big bags, the PET flakes are sold to drinks manufacturers and bottling companies, thus completing the cycle. In the bottling plants, the flakes are mixed and melted together with virgin PET. The liquid material is used to create what are known as preforms, the neck and thread of which are already the correct size for the new bottles.
After another quality check, the preforms are heated to up to 250°C by means of infrared light, inflated, stretched and thus brought into the final bottle shape. Before filling directly at the source, each bottle is checked for cleanliness, shape and impermeability. Once they have been sealed and labelled, the bottles are returned to retail and the cycle starts all over again.