The numbered components are described in detail in the following listing:
1. Bale feed
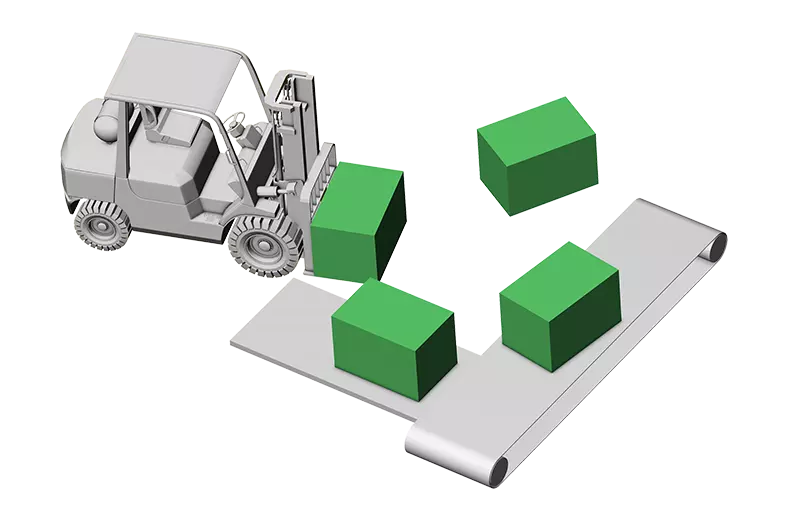
In the first stage, the PET bottles are pre-sorted and foreign objects such as metals, tins and other contaminants are separated from the PET and then sorted according to colour. The process for food-grade PET only uses clear bottles for processing.
2. Bale dissolver
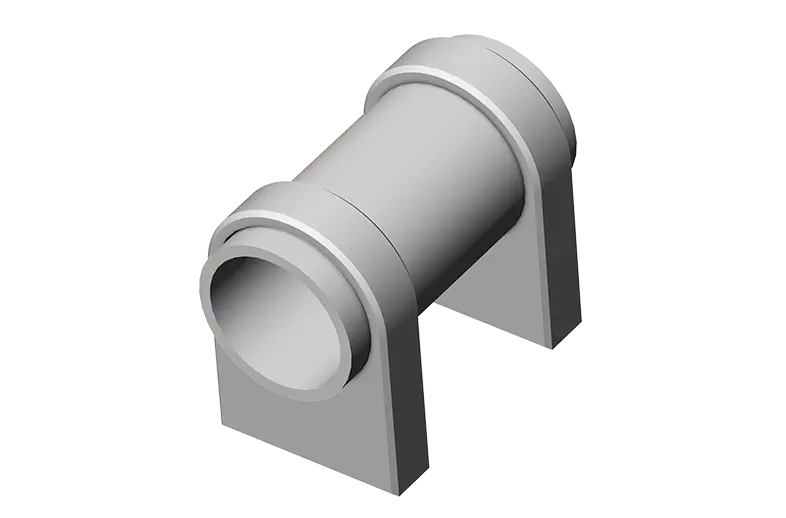
The clear PET bales are separated by the bale dissolver. In this step, the bottle caps pass through a drum sieve that sorts them.
3. Sorting booth
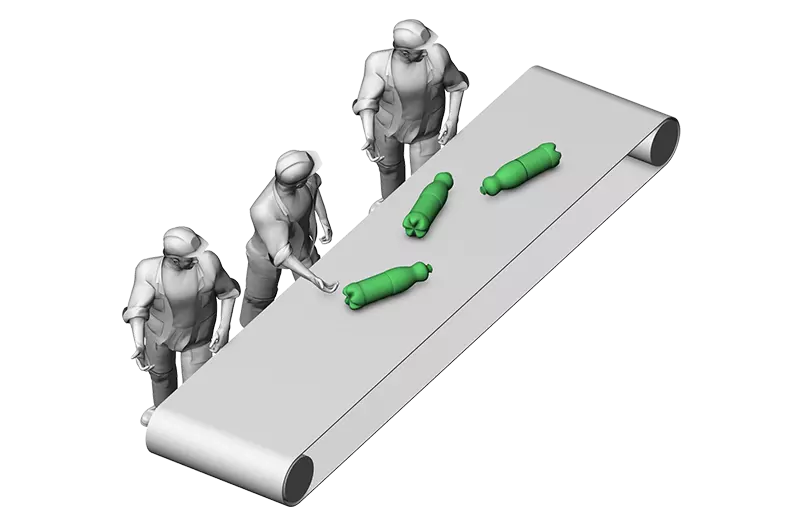
A staff member inspects the clear PET bottles again manually and removes any remaining contaminants.
4. Grinder
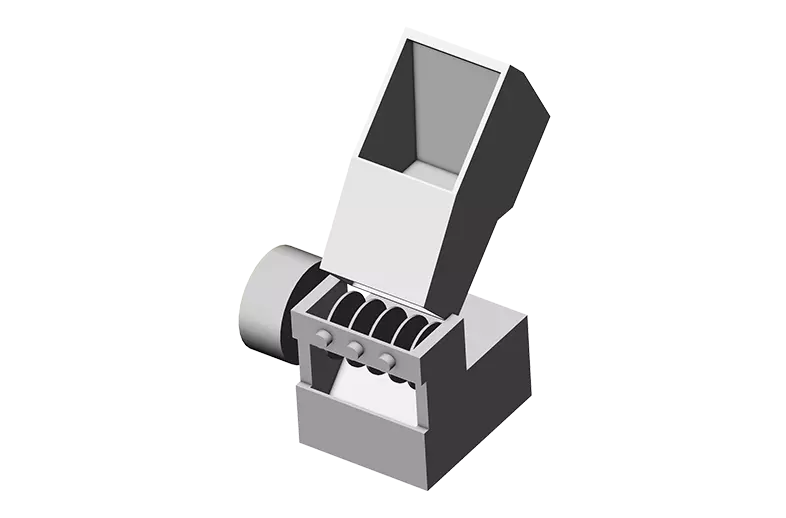
A mill grinds the clean bottles into flakes.
5. Hot wash
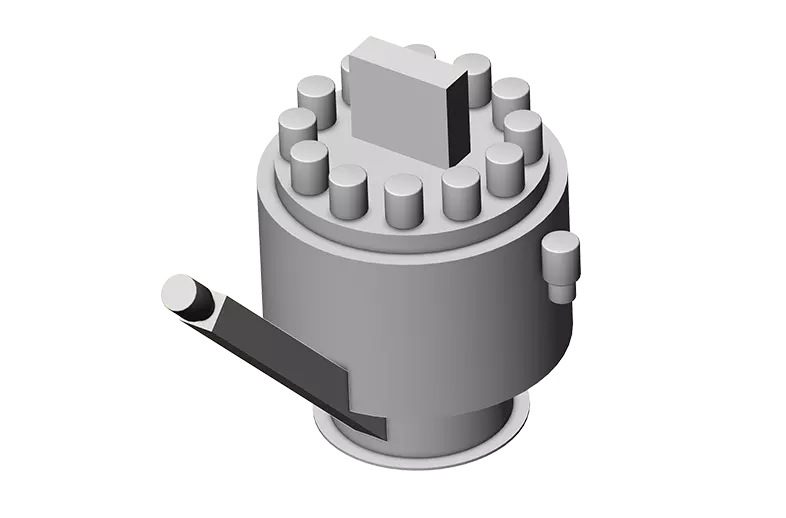
Hot water mixed with an alkaline solution cleans the flakes of labels and drink residue as well as large dirt particles.
6. Swim-sink separation
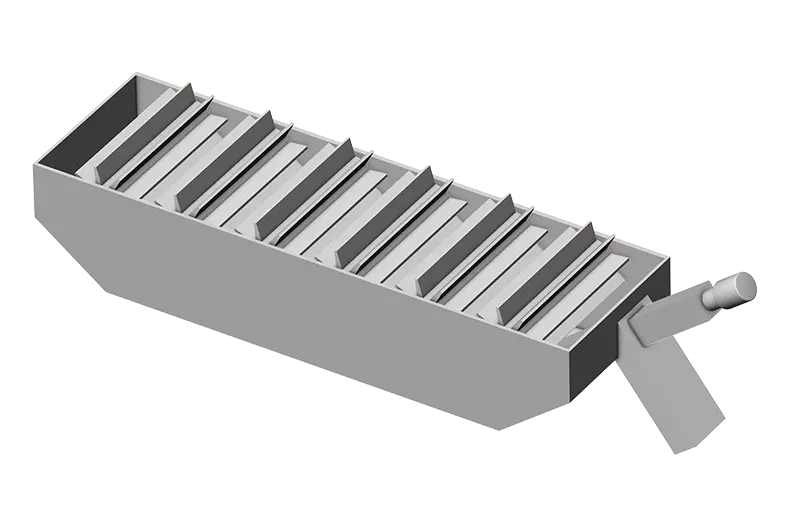
After the hot wash, the material lands in a swim-sink separation tank where the different types of plastic are separated from each other using their physical density. The HDPE and PP plastics float to the surface and the PET sinks to the bottom of the tank. This process separates HDPE and PP as a raw material for new caps from the PET flakes.
7. Drying
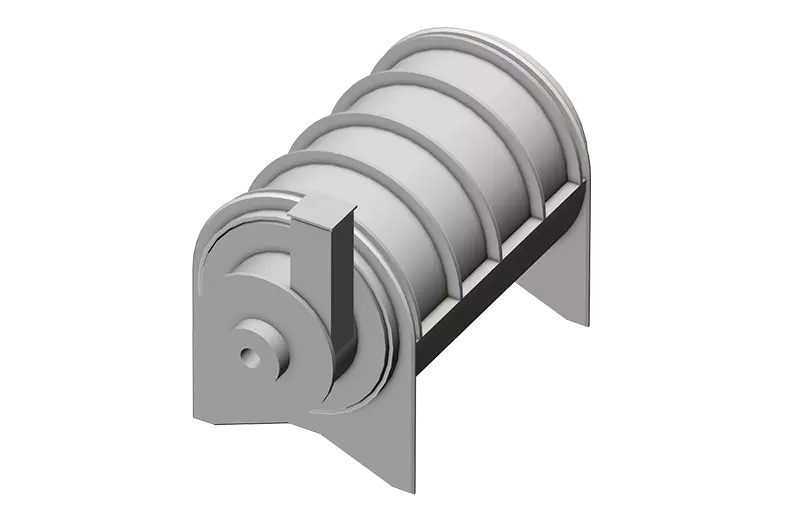
The PET material is dried to facilitate further processing.
8. Air classifier
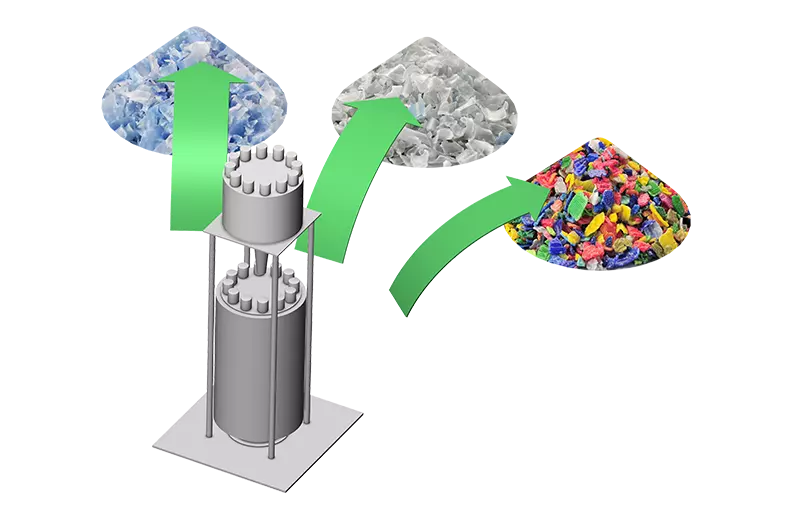
By using an air classifier, small foreign particles such as multilayer films or labels can be removed. The washed flakes are then further processed in non-food applications.
9. Caustic soda treatment
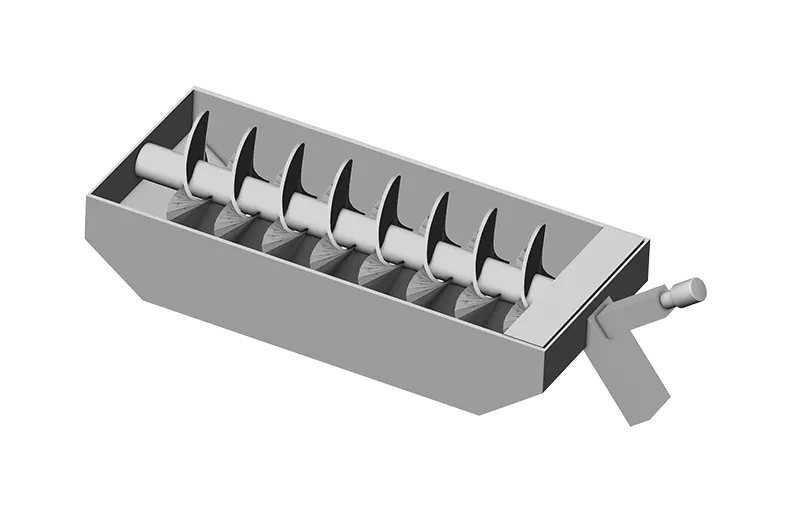
The washed flakes produced are further processed as input material for manufacturing food-grade flakes. A special device moistens the washed flakes with caustic soda to later achieve a "peeling effect" on the exterior of the flakes.
10. Surface cleaning with vacuum treatment
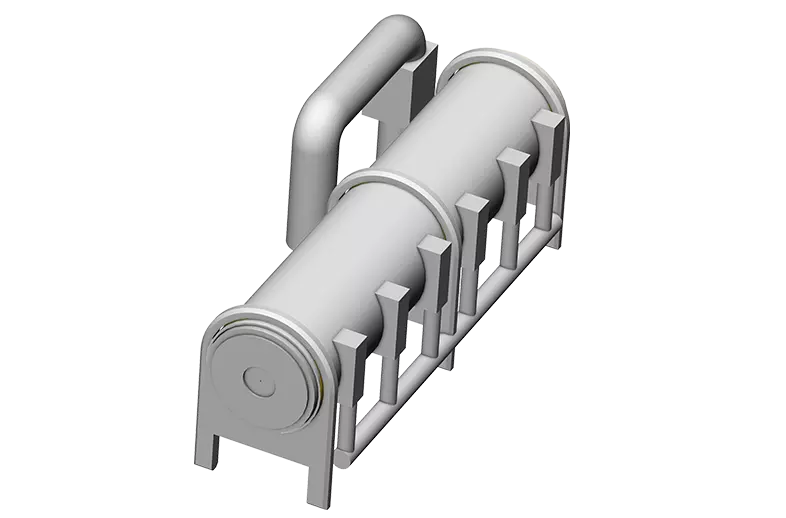
Once the material has been dried, it goes into a rotary kiln which sterilises the surface once again whilst also removing any odorants. Because the PET materials are not melted, the polymer chains remain completely intact.
11. Rewash and drying
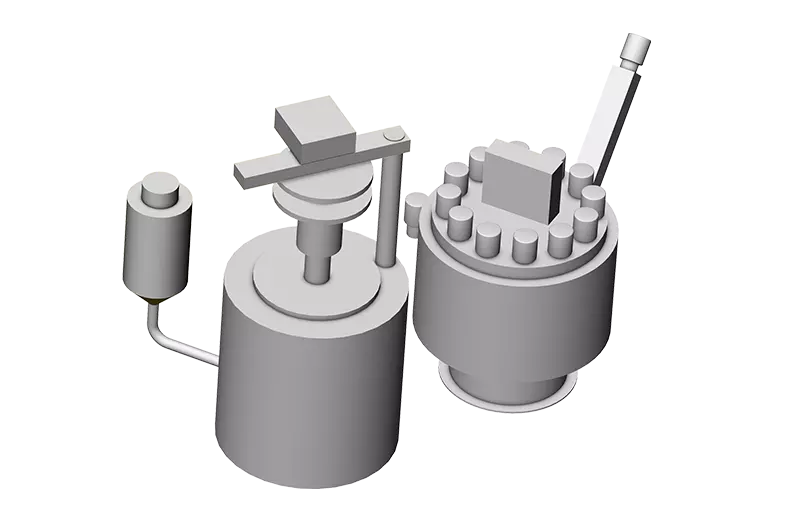
The salt formed during this process is sieved and washed out. In addition, the material is neutralised and then dried.
12. Sieving and sorting

The flakes are now food-grade and are sieved to remove oversized and fine particles. A colour sorter then separates any remaining colour PET flakes and foreign particles. Foreign materials such as PVC or nylon discolour and can therefore easily be sorted out. A laser sorting system is also able to recognize foreign particles which are not discoloured and separates the finest foreign particles.
13. Filling
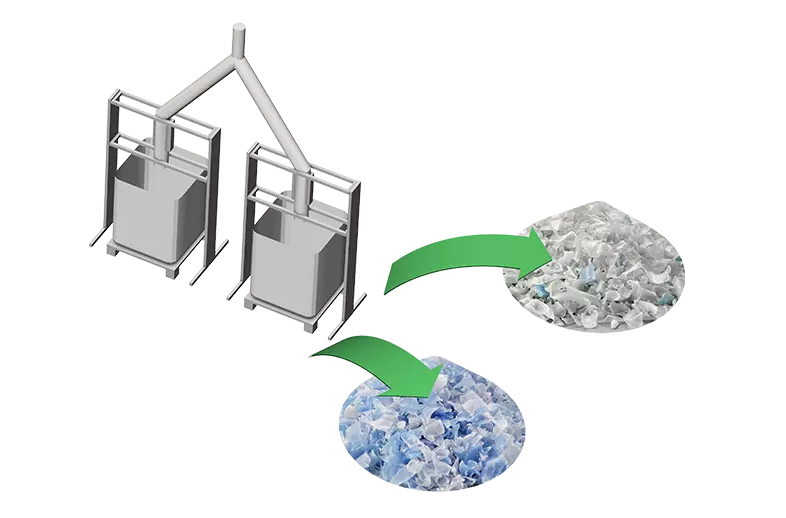
The pure PET materials is filled in big bags for transport. The food-grade flakes are ready (CleanPET® FK).